Os fornos de mufla são um design, cujos elementos de aquecimento permitem atingir a temperatura necessária para queimar cerâmica, fundir metais, endurecer aço em uma oficina pessoal. Joalheiros e outros artesãos cuja oficina é em casa entendem o valor de tal design. E dado o alto custo dos fornos de mufla produzidos na fábrica, tal forno, feito de forma independente, é de particular importância.
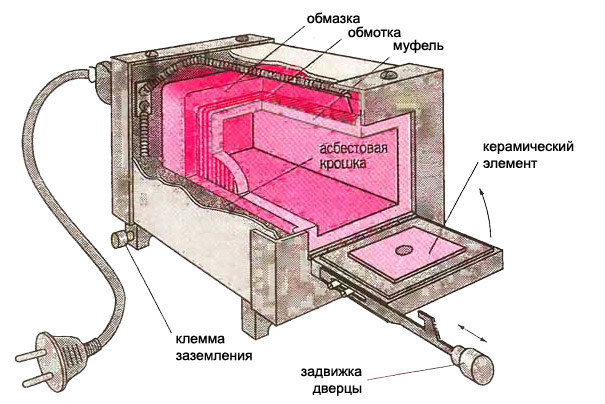
O dispositivo do forno elétrico mufla
Contente
Classificação dos fornos de mufla
De acordo com o tipo de elementos de aquecimento, os fornos de mufla são divididos em:
- elétrico;
- gás.
Por finalidade, eles são divididos em:
- para derreter metal;
- para queima de cerâmica;
- para derreter vidro;
- para endurecimento de metal;
Existem também fornos de mufla industriais e caseiros.
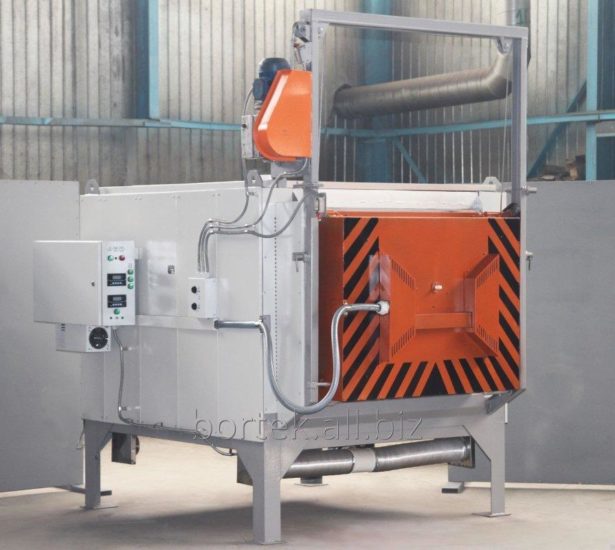
Forno de mufla industrial com automação
Mas é impossível fazer fogões a gás em casa, embora o gás seja mais barato que a eletricidade, pois tais experimentos são proibidos por lei. O controle elétrico do forno proporciona a conveniência do controle de temperatura.
Por tipo construtivo, os fornos mufla são divididos em:
- horizontal (o mais simples);
- tipo vertical ou pote;
- em forma de sino;
- tubular.
O aquecimento pode ser realizado ao ar, em vácuo ou em meio gasoso.Em casa, só é possível projetar um forno com tratamento térmico de produtos em ambiente de ar.
Com a implementação independente do forno de mufla, ele pode receber a forma e o volume desejados, decorados em um estilo adequado ao interior.
As principais partes da estrutura
- A parte externa do forno, o invólucro (invólucro) Como alojamento para o futuro forno mufla, é conveniente usar um fogão a gás em desuso, ou melhor, um forno dele ou um fogão elétrico. Para usá-los, todas as peças plásticas são desmontadas. No caso de não ser possível usar essas opções de caixa, ela é soldada em chapa de metal (pelo menos dois milímetros de espessura).
- Camada de isolamento térmico. Esta parte do design é extremamente importante. A eficiência do forno e a perda de calor que incorrerá depende de sua qualidade. A camada interna de isolamento térmico é um tijolo refratário (fireclay) que pode suportar temperaturas de até mil graus.
- A camada externa, que reduz a perda de calor para o espaço circundante, é feita de perlita ou lã de basalto. O amianto não é seguro de usar; quando aquecido, substâncias cancerígenas são liberadas na atmosfera.
- Elementos que aquecem diretamente o espaço de trabalho. Os elementos de aquecimento dentro do forno mufla são espirais torcidas de arame nicromo ou fechral. Espessura 1 mm. O fio de nicromo (níquel-cromo) é muito dúctil e resistente à corrosão.
- O fio fechral (alumínio, cromo, ferro) é um pouco mais barato devido à ausência de alumínio na composição e também possui as propriedades necessárias para seu uso em um forno mufla.
Lista de materiais e ferramentas para montar a estrutura
- esmerilhadeira (máquina para retificar e cortar materiais) com discos de corte para metal;
- máquina de solda;
- chapa de aço >2mm de espessura;
- cantos metálicos;
- tijolo refratário à prova de fogo;
- mistura refratária;
- silicone resistente ao calor;
- isolante térmico de basalto (lã, densidade 200 kg/m3) ou perlita;
- óculos e respirador;
- fio de nicromo (fechral) com seção transversal de 1 mm;
- alicates ou tesouras para metal.
Tecnologia de construção de forno de mufla
O procedimento para realizar o trabalho de um forno de mufla horizontal ou vertical é semelhante, a diferença está no arranjo dos elementos do forno.
- O corpo do forno mufla é feito de chapa de ferro. Recortamos uma tira retangular do tamanho necessário com um moedor, dobramos em um raio e selamos a costura com a ajuda de soldagem. Para evitar a formação de corrosão, você pode cobrir o metal com várias camadas de tinta refratária. Soldamos o fundo ao cilindro resultante. Para fazer isso, cortamos um círculo do diâmetro necessário de uma chapa de aço, igual ao diâmetro do cilindro. Reforçamos as paredes e o fundo com ferragens metálicas. O corpo é feito de tal volume que é possível colocar uma camada protetora de calor e tijolos refratários no interior.
- Se uma geladeira antiga for usada para o gabinete, também fortalecemos o fundo e as paredes com cantos ou tubos de metal.
- Colocamos a parte interna do corpo com uma espessa camada de lã de basalto.
- Para a fabricação da camada térmica interna (acumulador de calor) usamos tijolos refratários (refratários). A tarefa é juntar os tijolos na quantidade de sete peças na forma de um tubo, que mais tarde servirá como câmara de trabalho do forno.
- Para fazer isso, colocamos o tijolo em uma fileira e fazemos marcações em cada tijolo, ao longo das quais cortaremos. A forma dos tijolos após o corte deve permitir que todos os tijolos sejam montados na forma de um tubo oco. A poda é feita por um moedor. Por conveniência, os tijolos são numerados. Após o corte, nós os juntamos e os fixamos com arame, verificando a exatidão do corte. Se necessário, corrigimos o formulário, obtendo precisão.
Importante! Ao cortar tijolos, certifique-se de proteger seus olhos e órgãos respiratórios da poeira com óculos de proteção e um respirador. O trabalho deve ser realizado ao ar livre ou em uma área bem ventilada.
Colocamos o tubo de tijolo formado no corpo com uma camada de isolamento térmico.
Em seguida, na superfície interna dos tijolos, é necessário cortar ranhuras para o fio.
Mas primeiro, a partir de uma bobina de fio nicromo ou fechral, é necessário fazer uma espiral com um diâmetro de cerca de 6 mm. Para fazer isso, enrolamos o fio na base (lápis, eletrodo de solda ou haste de metal fina), retiramos os tijolos e os colocamos novamente em uma superfície plana em uma fileira.
Aplicamos uma espiral, fazemos marcações para sulcos futuros, que cortaremos em tijolos com um moedor. Verificamos a exatidão das linhas com um nível de construção. Por fim, dentro do espaço de trabalho, o fio será colocado em espiral de baixo para cima. É importante que as curvas não se toquem, caso contrário haverá um curto-circuito.
Para trazer as extremidades do fio para fora da câmara de trabalho e conectá-las à máquina, entre dois tijolos adjacentes, inserimos três peças finas e longas de ladrilhos cerâmicos com canais finos serrados para o fio.
O uso desses cabos cerâmicos no futuro facilitará o reparo do forno mufla.
Comutação elétrica com três níveis de potência
- para o primeiro estágio de energia, é necessário conectar dois circuitos de bobina em série;
- o segundo estágio implica uma conexão separada da espiral inferior;
- o terceiro estágio de energia é a conexão paralela de dois circuitos.
Ao ligar as espirais, o aterramento é obrigatório!
Colocamos a estrutura acabada da câmara de trabalho em uma caixa com uma camada de material isolante de calor e um tijolo colocado no fundo, revestindo-o com argila refratária (forno) ou cola refratária.
Para trazer os canais cerâmicos para fora do gabinete, fazemos furos nele.
Fazemos a cobertura de chapa de aço, cortando-a no tamanho do forno e fixando tijolos refratários nela com argila do forno. De cima, soldamos o pedaço, alças e coberturas. Para estanqueidade, aplicamos uma camada de silicone resistente ao calor ao longo das bordas da tampa e nas paredes adjacentes do forno mufla, tendo previamente desengordurado completamente as superfícies.
Depois que o forno estiver completamente seco, ligamos o fio a uma máquina elétrica com estabilizador e realizamos uma série de testes, ajustando a potência de aquecimento das espirais e a temperatura no local de trabalho, aumentando ou diminuindo a tensão da rede.
Importante! Para certificar-se de que a estufa está completamente seca, ligue-a na potência máxima e verifique se não há saída de vapor das superfícies da estufa.
A porta deve estar bem fechada enquanto o forno estiver em funcionamento.
Vídeo - forno de mufla caseiro