Vielleicht ist kein gemütliches Privathaus ohne einen guten Ofen oder Kamin vorstellbar. Außerdem sind viele Menschen, die in nicht vergaseten Gebieten leben, bis heute gezwungen, einfach mit Brennholz zu heizen.
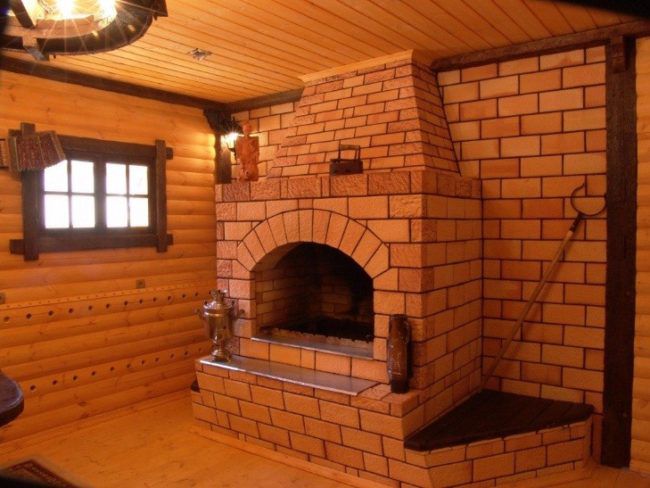
Ziegelmörtel für Ofenanteil
Dies ist einerseits die umweltfreundlichste Art des Heizens und andererseits kostengünstig. Die Preise für alternative Kraftstoffe und Strom steigen stetig, daher ist es notwendig, nach dem besten Ausweg aus dieser Situation zu suchen.
Viele Menschen wollen Öfen verlegen lernen, und das liegt nicht nur an dem Wunsch, im Winter beim Heizen Geld zu sparen. Die während der Ausbildung erworbenen praktischen Fähigkeiten können eine hervorragende Hilfe bei der Entwicklung eines persönlichen Unternehmens sein. Die Nachfrage nach Ofenarbeiten wächst jedes Jahr und schafft Aussichten auf ein ziemlich hohes Einkommen.
Inhalt
- Hitzebeständig, hitzebeständig, feuerfest – was ist der Unterschied?
- Welche Lösungen werden beim Verlegen einzelner Elemente eines Steinofens verwendet?
- Arten von Mörtel für Maueröfen und ihre Haupteigenschaften
- Wie kann man Mauerwerksmaterialien sparen?
- Wie unterscheidet man hochwertigen Ton, der zum Verlegen eines Ofens geeignet ist, von anderen Fossilien?
- So finden Sie hochwertiges Wasser für Ofenmauermörtel
- Welche Art von Sand ist zum Verlegen des Ofens geeignet? Sandvorbereitung
- Die Proportionen des Mörtels zum Verlegen des Ofens, wie viel Sand, Wasser und Ton sollten sein?
- Proportionen und richtige Zubereitung von Lehmmörtel, Festigkeitsprüfung
- Richtige Vorbereitung des Mörtels zum Verlegen des Ofens: Videolektion
- Video: So bereiten Sie eine Tonzusammensetzung zum Verlegen eines Ofens vor
Hitzebeständig, hitzebeständig, feuerfest – was ist der Unterschied?
Ofenbauer-Anfänger haben oft Schwierigkeiten, die Terminologie richtig zu verstehen. In Bezug auf Mörtel für Ofenmauerwerk entsteht die größte Verwirrung mit den Begriffen Hitzebeständigkeit, Hitzebeständigkeit und Feuerbeständigkeit des Materials. Diese Parameter sind im Ofengeschäft von grundlegender Bedeutung, daher werden wir nun versuchen, ihre Bedeutung zu klären und das Verständnis dieses Problems zu klären.
hitzebeständig ist ein Material, das einer Erwärmung auf hohe Temperaturen standhalten kann. Gleichzeitig bleiben beim anschließenden Abkühlen Struktur und chemische Zusammensetzung erhalten und es treten keine irreversiblen Formänderungen auf. Darüber hinaus sind hitzebeständige Materialien im erhitzten Zustand noch in der Lage, der ursprünglich spezifizierten physikalischen Belastung ohne die Gefahr einer möglichen Zerstörung standzuhalten.
Haupteigentum hitzebeständig Materialien - Beständigkeit gegen Temperatureinflüsse, sofern die ursprünglichen mechanischen Eigenschaften erhalten bleiben. Hitzebeständige Stoffe und Verbindungen haben eine um eine Größenordnung geringere Wärmeausdehnung als hitzebeständige.Solche Materialien werden nicht nur bei der Konstruktion von Öfen, sondern auch von mechanischen Geräten verwendet, die unter extremen Temperaturbedingungen arbeiten und gleichzeitig starken dynamischen Effekten ausgesetzt sind.
Endlich, feuerfest Materialien sind hitzebeständige oder hitzebeständige Verbindungen, die unter anderem der Einwirkung chemisch aktiver (oft aggressiver) Stoffe, die in gasförmigen Stoffen enthalten sind, problemlos standhalten. Speziell bei Ofenmauerwerk kann es sich dabei um Rauch oder Produkte der thermischen Zersetzung von Brennstoff handeln.
Alle beim Ofenbau verwendeten Lösungen und Materialien müssen hitzebeständig und feuerfest sein. Diese Anforderung gilt auch für solche Elemente, die sich im normalen Betrieb des Ofens nicht um mehr als vierhundert Grad erhitzen. Keine Standard-Baumischung erfüllt diese Parameter.
Welche Lösungen werden beim Verlegen einzelner Elemente eines Steinofens verwendet?
Die Wahl des Mörtels für die Arbeit muss in Abhängigkeit davon erfolgen, welcher Teil des Ofens zum Verlegen verwendet wird. Lassen Sie uns anhand des folgenden Diagramms einen genaueren Blick auf jeden von ihnen werfen.
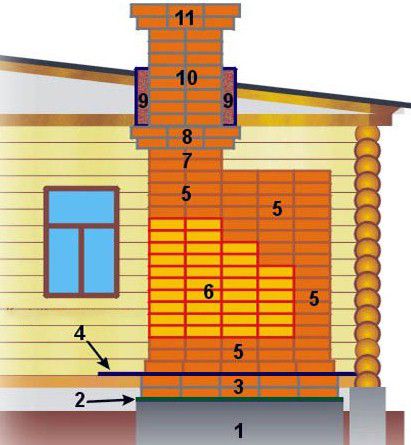
Allgemeines Strukturdiagramm eines Standardofenmauerwerks
- Sockel aus Stahlbeton Ofenfundament, die auch Kissen oder Wurzel genannt wird. Es wird jedoch nach Standardtechnologie hergestellt, um unangenehme Folgen zu vermeiden, muss es physisch vom Fundament des Hauses selbst getrennt werden. Die Notwendigkeit, diese Bedingung einzuhalten, erklärt sich aus Unterschieden im Schrumpfungsgrad des Gebäudes und des darin enthaltenen Ofens.
- Wasserdichte Schicht. Um es zu schaffen, ist Dachmaterial perfekt, das in mehreren Schichten auf das Fundament gelegt werden muss.
- Eigentlich das Ofenfundament selbst. Da es keinen starken thermischen Einwirkungen ausgesetzt ist, erfordert es beim Mauern keine Verwendung besonders hitzebeständiger Mischungen. Gleichzeitig hängt die Zuverlässigkeit der gesamten Struktur von der Qualität der Montage dieses Ofenelements ab. Es gibt Fälle, in denen es aufgrund von Fehlern beim Verlegen des Fundaments erforderlich war, den Ofen vollständig zu zerlegen und auf neue Weise zu erneuern. Gearbeitet wird mit komplexen, drei- oder mehrkomponentigen Zement-Kalk-Mischungen. Nun, als Hauptbaustoff ist hier roter Vollziegel am besten geeignet.
Für die Herstellung von Kompaktöfen oder Öfen mit großer Stellfläche (z. B. ein russischer Ofen) können Sie auch eine herkömmliche Kalkmischung verwenden.
- Eine Wärmedämmschicht mit Brandschutzbereich. Es besteht aus einer Mineralpappe oder Asbestplatte, auf die eine Eisenplatte gelegt wird, die die gesamte Struktur mit einer Endschicht aus Filztuch bedeckt, die in sogenannter Lehmmilch (dies ist eine Lösung aus sehr flüssigem verdünntem Lehm) getränkt ist , wie man es zubereitet - wir werden es weiter unten erzählen).
- Ein Wärmetauscher, der die bei der Verbrennung von Brennholz freigesetzte Energie akkumuliert. Es ist eines der Hauptteile des sogenannten Ofenkörpers. Während des Anzündens wird es selten über sechshundert Grad erhitzt, aber es wird durch den Rauch und andere gasförmige Substanzen, die bei der Verbrennung entstehen, sehr aktiv beeinflusst. Nicht selten setzt sich schädliches Säurekondensat auf der Innenfläche des wärmespeichernden Mauerwerks ab. Ziegel wird hier speziell verwendet: Ofen, Marke M150, vollmundige Keramik rot. Die Ziegel werden mit einer einfachen Einkomponenten-Lehmlösung aneinander befestigt.Zu beachten ist, dass sich der Begriff „einfach“ nur auf die Zusammensetzung der Baumischung bezieht. Seine Vorbereitung ist ein ziemlich mühsamer Prozess, dessen Merkmale wir im Folgenden betrachten werden.
- Der Feuerteil des Ofenkörpers wird auch Ofen genannt. Es ist dem durchschnittlichen chemischen Einfluss von Gasen ausgesetzt, wird aber auf sehr hohe Temperaturen, bis zu 1200 Grad, erhitzt. Für Mauerwerk werden sogenannte Schamottesteine und feuerfester Mörtel vom Ton-Schamotte-Typ verwendet.
- Schornstein Quelle. Es besteht aus demselben Ziegel und wird mit demselben Mörtel befestigt, der in Absatz Nr. 5 angegeben ist, da dieses Element des Ofens denselben Temperaturen und chemischen Einflüssen ausgesetzt ist wie der wärmespeichernde Teil seines Körpers.
- Den Ofenkamin „aufplustern“. Seine Aufgabe ist es, eine flexible mechanische Verbindung herzustellen, die die Decke und den Schornstein selbst verbindet. Ermöglicht es Ihnen, eine Situation zu vermeiden, in der ein Absinken der Decke möglich ist. Die Flusen können separat repariert werden, es ist keine vollständige Demontage der gesamten Struktur erforderlich. Ziegel für Mauerwerk werden als Standardofen genommen, und ein Kalkmörtel ist ideal zum Verlegen dieses Teils des Ofens.
- Feuerfestes Schneiden ist eine spezielle Metallbox, die mit einer nicht brennbaren wärmeisolierenden Substanz gefüllt ist.
- Schornsteinrohr. Dieses Element ist Wind und Niederschlag ausgesetzt. Es erwärmt sich schwach, daher wird das Rohr aus einem normalen roten Ziegelstein verlegt. Für eine größere Zuverlässigkeit und Hitzebeständigkeit wird jedoch Kalkmörtel verwendet.
- Flusen des Kaminrohrs (11). Es besteht aus den gleichen Materialien, die beim Verlegen des Hauptteils des Rohrs verwendet werden.
Arten von Mörtel für Maueröfen und ihre Haupteigenschaften
Nachdem Sie den vorherigen Absatz des Artikels gelesen haben, haben Sie möglicherweise bemerkt, dass für die Verlegung verschiedener Komponenten des Ofens empfohlen wird, Ihren eigenen Mörteltyp zu verwenden, der für die Arbeit am besten geeignet ist. Schauen wir uns jeden von ihnen genauer an.
Lehmmörtel zum Verlegen des Ofens: die Vor- und Nachteile
Lehmmörtel ist der billigste Baustoff. Es kann in der Regel selbst beschafft und zu Hause zubereitet werden. Auf diesen Vorgang gehen wir später noch im Detail ein, da die Herstellung der Verbundbauteile selbst recht aufwendig ist und eine gesonderte Einweisung erfordert. Die Stärke der Tonlösung sowie ihre Hitzebeständigkeit ist mittel. Die Zusammensetzung hält Temperaturen bis zu 1100 Grad Celsius ohne Folgen stand. In Bezug auf die Feuerbeständigkeit ist Ton hier praktisch beispiellos: Er entzündet sich nicht und kann nur von Flusssäure und Fluorantimonsäure gelöst werden. Es hat auch absolute Indikatoren für die Gasdichte. Ein auf Lehmmörtel gefalteter Ofen kann sicher wieder zusammengebaut werden, da die mit Wasser angefeuchtete Mischung wieder sauer wird. Darüber hinaus ist ein solches Material nahezu unbegrenzt für die Arbeit geeignet: Ein mit einem feuchten Tuch bedeckter Behälter mit einer Lösung trocknet auch nach einigen Monaten nicht aus. Auf der anderen Seite ist dies auch sein Nachteil: Lehm ist für Mauerwerk im Außenbereich völlig ungeeignet.
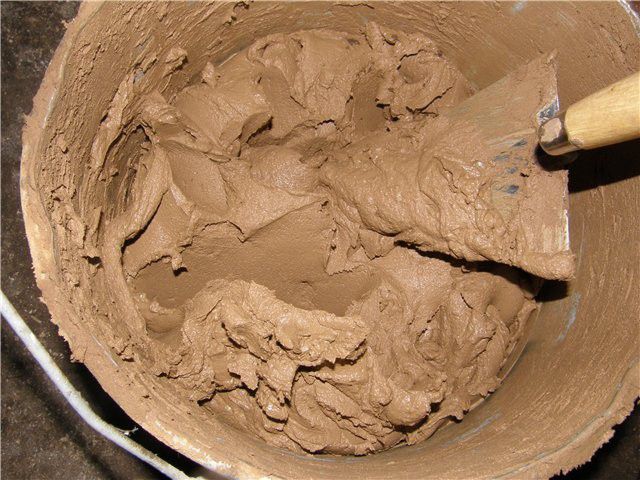
Das Aussehen der Tonlösung
Wie man einen Tonmörser zum Verlegen eines Ofens herstellt: Videoanleitung
Kalk und Zement-Kalk-Mischungen: Werden sie zum Verlegen von Öfen verwendet?
Granatwerfer
In jedem Fall kostet es mehr als Ton.Um es zuzubereiten, müssen Sie einen speziellen Limettenteig oder Branntkalk kaufen. Es sollte beachtet werden, dass Sie mit Branntkalk Geld sparen können, aber später wird es Sie mit erheblichen Arbeitskosten heimsuchen: Die Herstellung einer Lösung aus „kochendem Kalk“ ist ein gewissenhafter Prozess, da Sie alle Partikel löschen müssen letzte. Wenn Branntkalk in der Mischung vorhanden ist, dann kann die Mauerwerksnaht brechen. Der Mörtel selbst hat eine reduzierte Hitzebeständigkeit und Feuerbeständigkeit. Es ist in der Lage, inaktiven Rauchgasen mit Temperaturen unter fünfhundert Grad zu widerstehen. Im Vergleich zur Tonmischung hat es eine geringere Gasdichte. Andererseits nimmt Kalkmörtel keine Luftfeuchtigkeit auf, sodass Sie damit im Freien arbeiten können. Die fertige Mischung ist innerhalb einer relativ kurzen (im Vergleich zu Ton) Zeit verwendbar: Sie kann ein bis drei Tage nach dem Kneten auf den Ofen gelegt werden.
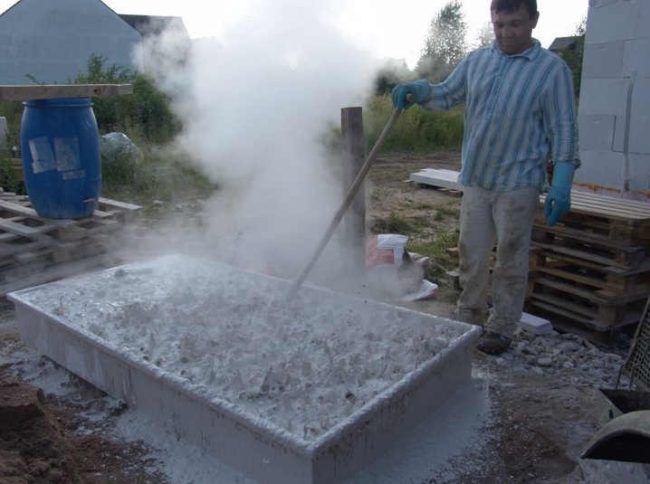
So sieht der Kalklöschprozess aus
Zement-Kalk-Mörtel
Es kostet mehr als gewöhnlicher Kalk. Dies wird jedoch teilweise durch seine erhöhte Festigkeit ausgeglichen. Dafür ist die Hitzebeständigkeit hier etwa doppelt so gering: Temperaturen bis 250 Grad hält das Zement-Kalk-Gemisch ohne Folgen aus. Der Gasdichteindex der Lösung ist gering. Es wird in den meisten Fällen für den Bau des Ofenfundaments verwendet. Es trocknet ziemlich schnell, so dass es seine Arbeitstauglichkeit nur innerhalb einer Stunde nach der Herstellung behält.
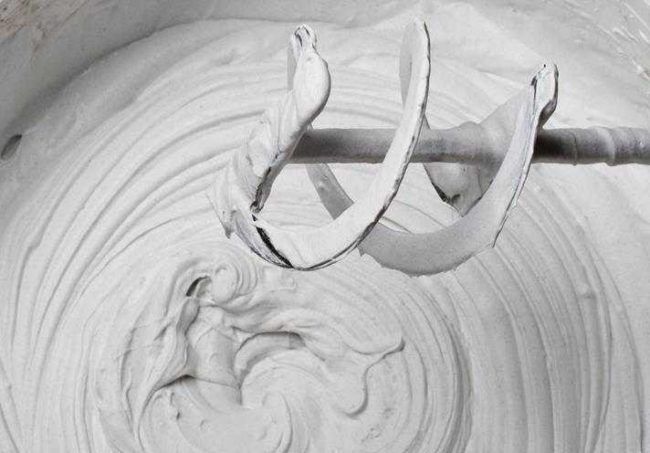
Aussehen von Kalkzementmörtel
Ton-Schamotte- und Zement-Schamotte-Lösungen
Ton-Schamotte-Mörser
Es hat alle Eigenschaften einer herkömmlichen Tonmischung, ist aber hitzebeständiger (seine maximale Betriebstemperatur erreicht 1300 Grad Celsius). Dieses Material ist natürlich teurer als Ton, da für seine Herstellung spezieller Schamottsand gekauft werden muss. Ton-Schamotte-Lösungen werden zum größten Teil für den Bau eines Ofenofens verwendet.
Zement-Schamotte-Mörtel
Es ist ziemlich teuer, weil es die Verwendung hochwertiger Komponenten erfordert. In Bezug auf die Festigkeit hat die Mischung die gleichen Indikatoren wie Zementkalk, während die Hitzebeständigkeit der eines Ton-Schamotte-Mörtels entspricht. Andererseits hat es einen durchschnittlichen Feuerwiderstand. Es reicht jedoch völlig aus, um den Ofenteil des Ofens zu verlegen. Die Haltbarkeit des fertigen Zement-Schamotte-Mörtels beträgt etwa vierzig Minuten. Das sollte auch beachtet werden Das Mischen der Komponenten darin erfolgt nicht manuell!
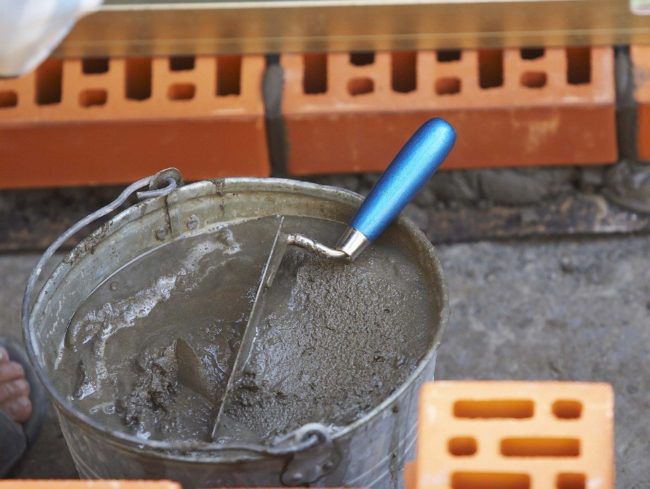
Aussehen von Zement-Schamotte-Mörtel
Die Namen von Mehrkomponenten-Mauerwerkmischungen werden üblicherweise so zusammengestellt, dass der Name des stärksten Bindemittels an erster Stelle steht. In diesem Fall kann der Prozentsatz seines Gehalts in der Lösung am kleinsten sein. Zum Beispiel ist Zement in einer Zement-Kalk-Mischung 10-15 mal weniger als Kalk.
Zwei oben verwendete Begriffe bedürfen einer gesonderten Erläuterung: „Gasdichtheit“ und „Schamotte“. Werfen wir einen Blick auf ihre Bedeutung.
Der Begriff "Gasdichte» gibt die Fähigkeit des Materials an, gasförmige Stoffe durchzulassen. Wenn die Lösung eine hohe Gasdichte hat, lässt sie keine Partikel heraus und sie gelangen aufgrund von Diffusion nicht in den beheizten Raum. Es sollte beachtet werden, dass Gasdichte und Hygroskopizität sich nicht gegenseitig ausschließen.Wasserdampfmoleküle sind kleiner und beweglicher als Rauchpartikel. Eine qualitativ hochwertige Lösung muss beide Qualitäten, sowohl Gasdichtheit als auch Hygroskopizität, in optimalen Anteilen kombinieren. Der Ofen muss "atmen" und darf gleichzeitig keinen Rauch hereinlassen. Diese Anforderungen sind der Schlüssel zur Formulierung von Mischungen für den Ofenbau.
Was das zweite betrachtete Konzept betrifft,Schamotte“wird als spezielles feuerfestes und hitzebeständiges Material bezeichnet. Es wird durch Tiefbrennen einer Mischung aus speziellem Ton (dem sogenannten "High Alumina"), Zirkoniumverbindungen, Granatkristallen und einigen anderen Komponenten hergestellt. Der Tiefbrand unterscheidet sich vom üblichen dadurch, dass er auch nach vollständiger Freisetzung des gesamten Kristallwassers aus dem Stoff für eine weitere Erwärmung bis hin zur Versinterung und Klumpenbildung sorgt.
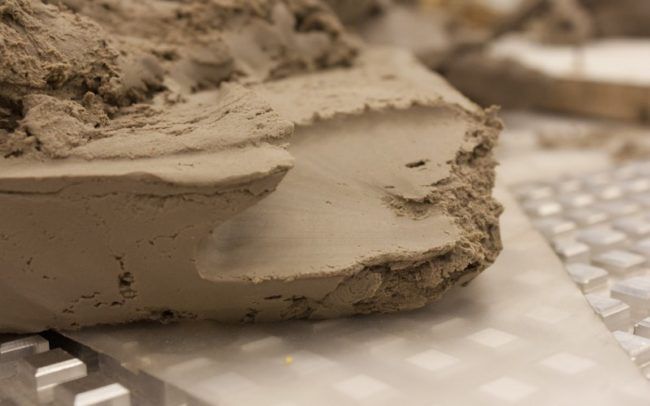
So sieht Schamotteton aus
Wie kann man Mauerwerksmaterialien sparen?
Die Antwort auf diese Frage scheint ganz offensichtlich zu sein: Es ist notwendig, das Beste aus den vorhandenen Materialien zu machen, die direkt auf der Baustelle des Ofens kostenlos erhältlich sind. In unserem Fall können wir selbst die folgenden Komponenten erhalten: Ton, Sand und Wasser. Aber wie die Praxis zeigt, ist in Wirklichkeit alles andere als so einfach. Sie können nicht einfach irgendein Wasser nehmen, es mit dem ersten Sand und Ton mischen, der auftaucht, und als Ergebnis eine gute Mischung für Mauerwerk erhalten. Für jede Komponente zur Herstellung eines Ofenmörtels werden eine Reihe ernsthafter Anforderungen gestellt. Lassen Sie uns mehr über jeden von ihnen erfahren und lernen, wie Sie alle erforderlichen Komponenten auswählen.
Wie unterscheidet man hochwertigen Ton, der zum Verlegen eines Ofens geeignet ist, von anderen Fossilien?
Tonbruch ist oft günstig bei lokalen Ofenbauern zu bekommen, aber wir empfehlen Ihnen nicht, den einfachen Weg zu gehen. Solches Material ist in der Regel stark mit organischen Verunreinigungen verunreinigt. Anschließend verrotten und zersetzen sie sich, was die Konsistenz der Mischung und die Qualität der fertigen Nähte verschlechtert. Es ist viel rentabler, guten Ton in der Umgebung zu finden und ihn selbst zu graben. Die Schwierigkeit liegt nur darin, zu lernen, hochwertige Ablagerungen von kontaminierten zu unterscheiden.
Ton ist im Wesentlichen eine Mischung aus Aluminiumoxid Al2Ö3 und Siliziumoxid SiO2 (einfach gesagt, Sand). Der wichtigste bestimmende Parameter für Ton ist sein Fettgehalt. Die Stärke seiner Struktur, Plastizität, Adhäsionsindikatoren (die Fähigkeit, an anderen Oberflächen zu haften), Hygroskopizität und sogar Gasdichtigkeit hängen wiederum direkt davon ab. Als Standard wird der Fettgehalt von Ton mit 62 Prozent Aluminiumoxid und 38 Prozent Sand gleich 100 % genommen, und der Fettgehalt von reinem Sand ohne Verunreinigungen wird als Nullbezugspunkt genommen - 0 %. Um den Mörtel zum Verlegen des Ofens zu kneten, benötigen wir Ton mit einem durchschnittlichen Fettgehalt, da die Nähte eines Materials mit einem zu hohen Fettgehalt beim Trocknen reißen. Auch „fettarmer“ oder auch „magerer“ Lehm ist nicht haltbar.
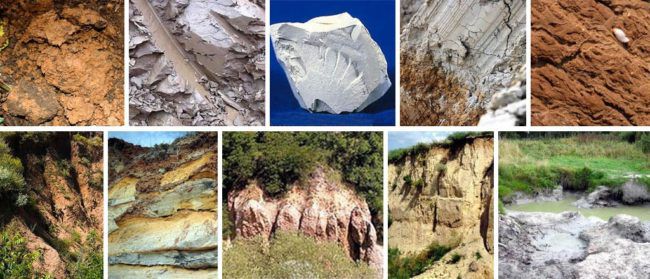
Tonablagerungen verschiedener Art
Clay hat mehrere fossile Zwillinge, die oft damit verwechselt werden. Ofenarbeiten mit anderen mineralischen Materialien sind jedoch nicht möglich, daher ist es wichtig, sie von dem unterscheiden zu können, was wir brauchen.
Tonschiefer und Mergel.Das Material ist ein sprödes Gestein. Es liegt in horizontalen Schichten, die für das Auge sichtbar sind und abgerundete Kanten haben. Wenn Sie außerdem eine Schieferprobe nehmen und sie brechen, zeigt der resultierende Abschnitt deutlich die Schieferstruktur.
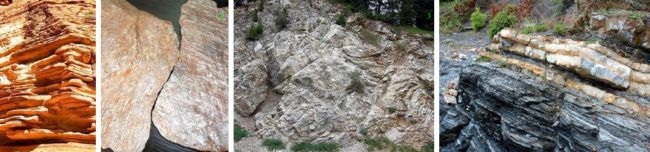
Aussehen von Schiefer
Am schwierigsten zu identifizieren ist Bentonit, auch bekannt als Bentonit-Ton (Bentoglin). Dies ist ein wertvoller Rohstoff, der jedoch für den Einsatz im Hochofengeschäft völlig ungeeignet ist. Manchmal gibt es Bentonit in leuchtenden Farben, der tatsächlich identisch aussieht mit dem Ton, den wir brauchen.
Bentonit-Ton, bestehend aus Natrium-Calcium-Verbindungen, Montmorillonit und anderen Verunreinigungen, hat seine Verwendung in der Pharmakologie, Medizin, Parfümerie, Weinherstellung und sogar im Bergbau gefunden. Die Einzigartigkeit dieser Mineralverbindung liegt in ihrer Fähigkeit, Feuchtigkeit aufzunehmen. Mit Wasser gesättigter Bentonit kann ohne Folgen um das Dutzendfache an Volumen zunehmen und in einen gelartigen Zustand übergehen. Aber leider besitzt es nicht die Eigenschaften von gewöhnlichem Ton, wie Feuerbeständigkeit, Gasdichtheit und Hitzebeständigkeit. Bentoglin ist ganz einfach von dem Baustoff zu unterscheiden, den wir brauchen. Es reicht aus, eine kleine Testprobe zu nehmen und sie in ein mit Wasser gefülltes Glas zu geben. Nach kurzer Zeit nimmt Bentonit Feuchtigkeit auf und nimmt merklich an Größe zu. Nach ausreichender Wartezeit können Sie die Umwandlung der Probe in ein Bentonit-Gel beobachten, das wie Gelee aussieht, etwas Gelee ähnlich. Aus Ton im Wasser wird so etwas nicht.
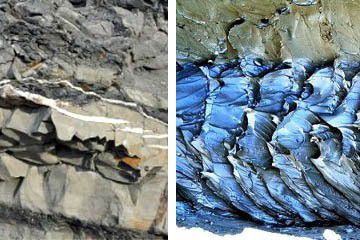
Aussehen von Bentonit-Ton
In der folgenden Abbildung sehen Sie einen schematischen Ausschnitt der für unser Land typischen Bodenstruktur. Ton in den oberen Erdschichten ist stark mit organischen Verunreinigungen belastet. Von oben ist die Hauptschicht der Tonablagerungen mit dem sogenannten Lehm bedeckt - einer Erdschicht mit einer erheblichen Beimischung von Tonerde und Sand. Lehm ist im Diagramm gelb dargestellt. Tatsächlich hat die Hauptschicht aus Ton einen ungleichmäßigen Fettgehalt: Sie ist von oben minimal und wächst, während sie tief in den Boden einsinkt.
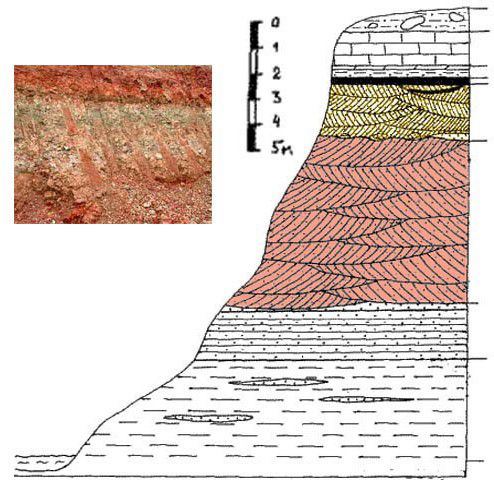
Schema der Anordnung von Tonschichten
Den Fettgehalt von Ton bestimmen wir anhand einer speziellen Probe. Rohstoffe für die Analyse müssen gesammelt werden, nachdem sie eine Lehmschicht passiert haben. In dieser Situation - ab fünf Meter von der Erdoberfläche entfernt.
Der Tontest selbst ist sehr einfach: Wir nehmen einen Materialklumpen mit einem Volumen von einer halben Faust in unsere Hände. Wir befeuchten unsere Hände mit Wasser und fangen an, es wie Plastilin zu kneten, wodurch die Probe allmählich die Form einer Kugel erhält.
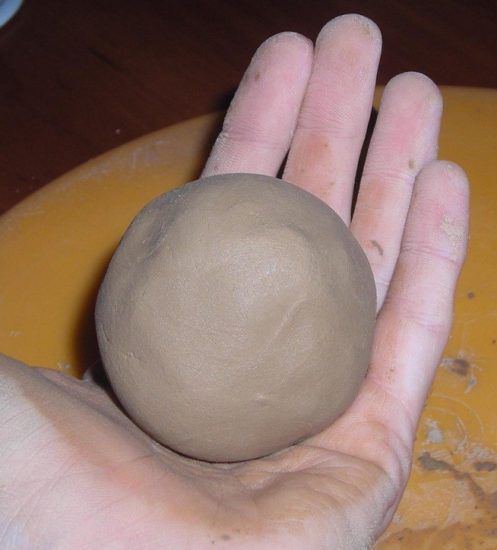
Musterkugel aus Ton gerollt
Nachdem die Kugel fertig ist, fangen wir an, sie mit zwei flachen Brettern auf beiden Seiten langsam genau so lange zu pressen, bis sich die ersten Risse bilden. Wenn Sie es geschafft haben, die Kugel um mindestens ein Drittel des Durchmessers zu komprimieren, ist ein solcher Ton für unsere Aufgaben gut geeignet. Etwa weitere fünf Kilogramm Material nehmen wir in einem Eimer und tragen es nach Hause für weitere Tests, auf die wir später noch zu sprechen kommen.
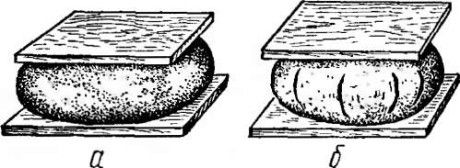
Überprüfung der Tonprobe mit Brettern
So finden Sie hochwertiges Wasser für Ofenmauermörtel
Es ist notwendig, die Qualitätsindikatoren des Wassers zu überprüfen, das wir zur Herstellung der Ofenlösung verwenden möchten.Zum Arbeiten ist nur sogenanntes „weiches“ Wasser oder zumindest Wasser mit mittlerer Härte geeignet. Die Härte wird in deutschen Graden gemessen. Ein solcher Grad bedeutet, dass in jedem Liter des untersuchten Wassers 20 Milligramm Calcium- und Magnesiumsalze enthalten sind. Das Kneten der Ofenlösung kann nur durchgeführt werden, wenn die Wasserhärte unter zehn Grad liegt.
Ein Experiment, mit dem Sie die Wasserparameter bestimmen können, erfordert den Kauf von etwa 0,2 Litern destilliertem Wasser in einer Apotheke. Wir nehmen auch ein Stück Waschmittel und zerbröckeln es in kleine Stücke. Es wird unser Indikator sein, da Seife die im Wasser gelösten Salze neutralisiert. Ein Gramm 72-prozentiger Standardseife neutralisiert etwa 7,2 Milligramm Härtesalze. Bis der Wasserenthärtungsprozess abgeschlossen ist, schäumt die Seifenlösung nicht. Dies zeigt uns, wie „hart“ das Wasser ist. | |
![]() Wasser erhitzen und Seifenkrümel dazugeben | Wir erhitzen destilliertes Wasser auf etwa 75 Grad und lösen die Seife vorsichtig darin auf. Dieser Vorgang sollte sorgfältig durchgeführt werden, um ein Schäumen der Mischung zu vermeiden. Die Proportionen, in denen unser "Indikator" hinzugefügt werden muss, sind wie folgt:
|
![]() Ziehen Sie eine Seifenlösung in die Spritze auf | Als Ergebnis erhalten wir, nachdem alles abgekühlt ist, die sogenannte "Titrationsmischung". Mit Hilfe eines Bechers sammeln wir etwa 500 Milligramm des getesteten Wassers und mit einer Spritze (ohne Nadel) 20 Milliliter der resultierenden Seifenlösung. |
![]() Wasser mit darin gelöster Seife | Die Lösung tropfenweise unter leichtem Rühren in das zu testende Wasser geben. Zunächst beginnt Seife, die mit Calcium- und Magnesiumsalzen interagiert, in Form von charakteristischen grauen Flocken auszufallen. Wir setzen den Prozess fort, bis sich ein Schaum mit regenbogenfarbenen Seifenblasen zu bilden beginnt. Mit dem Auftreten von Blasen hören wir auf, im Destillat gelöste Seife hinzuzufügen, und sehen uns an, wie viel Lösung wir benötigen, um alle Salze vollständig zu neutralisieren. Als nächstes führen wir einfache Berechnungen durch und ermitteln die Wasserhärte. |
Nehmen wir an, wir haben 100 % reine Seife verwendet, von der 10 Milliliter ein Gramm Seife enthalten. Diese Seifenmenge in 500 Milliliter getestetem Wasser sollte 10 Milligramm Mg- und Ca-Salze ausgefällt haben. Das bedeutet, dass ein Liter Wasser 20 mg Verunreinigungen durch Härtesalze enthält, was einem deutschen Grad entspricht. Und wenn wir 80 Milliliter seifige Titrationslösung ausgegeben haben, dann beträgt die Wasserhärte 8 Grad und es ist auch für Ofenmauerwerk geeignet. Die Hauptsache ist, den Steifigkeitsgrenzwert von 10-11 Einheiten nicht zu überschreiten. |
Welche Art von Sand ist zum Verlegen des Ofens geeignet? Sandvorbereitung
Was den Sand betrifft, müssen keine Proben genommen werden. Neben den Tonablagerungen findet man immer wieder Zwischenschichten aus weißem Quarzsand und gelbem, feldspathaltigem Sand. Der erste eignet sich zum Erstellen beliebiger Ofenstrukturen, und der zweite kann zum Verlegen aller Elemente mit Ausnahme des heißesten Teils - des Feuerraums - verwendet werden. Denken Sie daran, dass die Vorbereitung von Sand für die Arbeit eine erhebliche Menge Wasser erfordert. Deshalb sollten Sie sich schon im Vorfeld um die Klärung von Problemen bezüglich der unterbrechungsfreien Wasserversorgung kümmern.
Der allein anfallende Sand muss zunächst durch ein Sieb mit einer Maschenweite von 1-1,5 Millimeter geleitet werden. Auf diese Weise können Sie verschiedene große Trümmer entfernen und die erforderlichen Fraktionen erhalten. Das größte Problem für selbstgegrabenen Sand sind organische Verunreinigungen und verschiedene lebende Mikroorganismen, die darin leben. Der Sand muss von ihnen gereinigt werden, da sich sonst die Mauerwerksnähte mit der Zeit verschlechtern können.
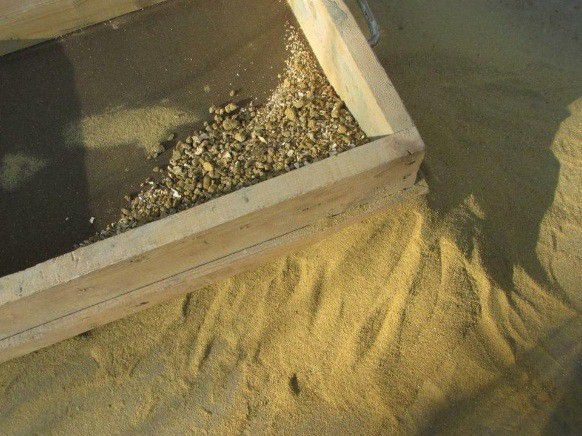
Sand mit einem Sieb sieben
Es gibt viele industrielle Sandreinigungsmethoden, aber alle sind mit erheblichen Energiekosten verbunden. Um Geld zu sparen, verwenden wir eine einfache und für alle zugängliche Waschmethode.
Für die Herstellung eines Reinigungsgerätes benötigen wir ein Rohrstück mit 15-20 Zentimeter Durchmesser. Seine Höhe sollte etwa das Dreifache seiner Dicke betragen. Wir füllen ein Drittel des Volumens mit Sand auf und führen Wasser unter Hochdruck von unten zu. Die Stärke des Wasserstrahls muss so gewählt werden, dass der gewaschene Sand verwirbelt wird, aber nicht in den darüber befindlichen Abfluss fließt. Nachdem sauberes Wasser in den Abfluss fließt, warten wir weitere zehn Minuten und beenden den Vorgang. Die erste Ladung gereinigter Sand ist fertig. Es bleibt nur zu trocknen.
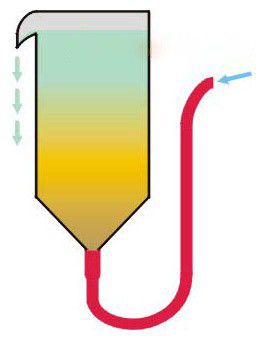
Schema der Vorrichtung zum Waschen von Sand
Die Methode des Filterns von Sand durch Waschen ermöglicht es Ihnen auch, verschiedene Einschlüsse von Aluminiumoxid daraus zu entfernen, die wir nicht benötigen.
Die Proportionen des Mörtels zum Verlegen des Ofens, wie viel Sand, Wasser und Ton sollten sein?
Ein wichtiger Schritt bei der Herstellung eines Bauofenmörtels ist die Bestimmung des optimalen Verhältnisses zwischen Sand und Ton. Nachdem wir die nach dem obigen Algorithmus ausgewählte Tonprobe nach Hause gebracht haben, muss sie in zwei Teile geteilt werden.Wir legen die erste Hälfte beiseite und teilen die zweite wieder in fünf identische Teile. Wir legen sie jeweils in eine separate Schale und fügen dort Wasser (Härte bis 11 Grad dt.) hinzu, etwa ein Viertel des Volumens des Tons selbst.
Als nächstes lassen Sie den Ton im Wasser hinken. Normalerweise dauert dieser Vorgang etwa 24 Stunden. Nach einem Tag gründlich umrühren und durch ein Sieb mit einer Maschenweite von drei Millimetern passieren, um große Klumpen auszusieben.
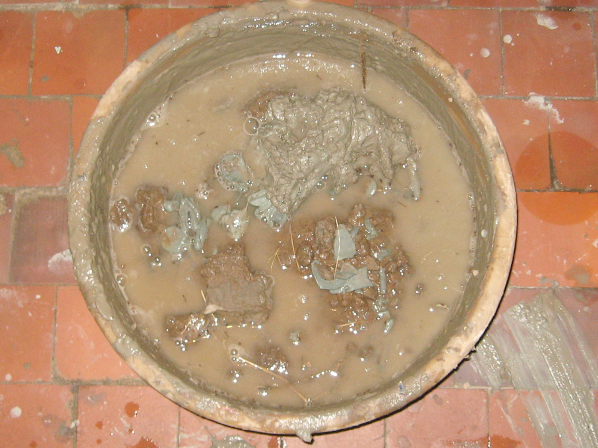
Ton sackt im Wasser ab
Wir stellen den Behälter mit der gesiebten Lösung wieder auf den Schlamm. Wenn nach dem Absetzen eine schlammige Aufschlämmung (der sogenannte „Schlamm“) auf der Oberfläche der Lösung erscheint, entfernen wir sie, indem wir sie auf den Boden gießen.
Alles, jetzt können Sie jedem Behälter mit vorbereitetem Ton Sand hinzufügen. Dies muss in den folgenden Anteilen erfolgen:
- Der erste Behälter - fügen Sie keinen Sand hinzu;
- Der zweite besteht aus einem Teil Sand und vier Teilen Ton;
- Der dritte besteht aus zwei Teilen Sand und vier Teilen Ton;
- Viertens - 3 Teile Sand und vier Teile Ton;
- Fünftens - Sand und Ton werden in gleicher Menge hinzugefügt.
Das Hinzufügen von Sand zu jedem der Behälter muss schrittweise in kleinen Portionen in mehreren Ansätzen erfolgen (optimal - mindestens drei und nicht mehr als sieben). Sie müssen alles sehr sorgfältig mischen. Beeilen Sie sich nicht, die nächste Portion Sand hinzuzufügen, bevor die vorherige vollständig und gleichmäßig in der Mischung aufgelöst ist. Einen gut angemischten Ton-Sand-Mörtel zu erkennen, ist ganz einfach: Versuchen Sie einfach, ihn zwischen den Fingern zu reiben. Wenn die Rauheit einzelner Sandkörner nicht zu spüren ist, ist alles richtig gemacht.
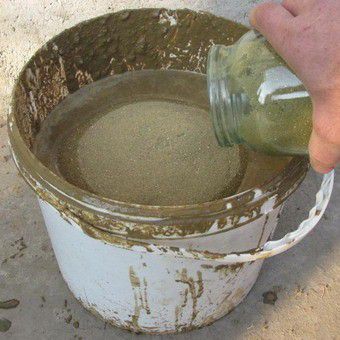
Füge Sand zu Ton hinzu
Der nächste Schritt bei der Herstellung des Ton-Sand-Mörtels wird die Herstellung von Prototypen sein.Wir nehmen Lehm in jeden der fünf Behälter und machen abwechselnd:
- Zwei Bündel von etwa 35 Zentimeter Länge und anderthalb Zentimeter Durchmesser;
- Wir formen eine Kugel mit einem Durchmesser von fünf Zentimetern;
- Ein runder Tonkuchen mit einer Dicke von 12-15 Millimetern und einem Radius von 7,5-8,5 Zentimetern.
Als Ergebnis haben wir genau 20 Proben zur Hand, die markiert und im Gebäude getrocknet werden müssen. Zur normalen Trocknung sollten die Proben keiner Zugluft und keiner direkten Sonneneinstrahlung ausgesetzt werden. Normalerweise trocknen die Kabel in ein paar Tagen aus, aber die Kuchen und Bällchen können bis zu zwei Dutzend Tage dauern. Wenn die Kugel nicht knittert und sich der Kuchen nicht mehr in zwei Hälften biegt, ist das Material vollständig ausgetrocknet.
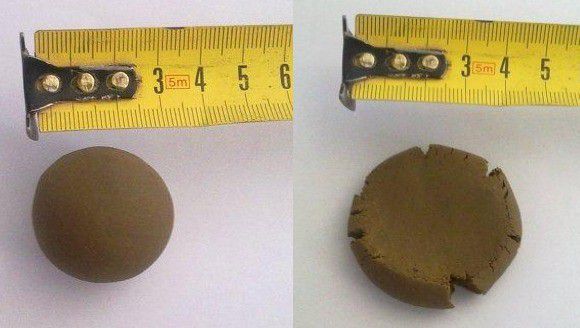
Tonkugel und Kuchen
Wenn die Proben zum Testen bereit sind, fahren wir mit dem nächsten klassischen Experiment fort, mit dem wir den Fettgehalt der Tonlösung bestimmen können. Dazu wickeln wir eine Aderpresse aus Ton um den Schaufelstiel, reißen ihn dann auseinander und beobachten das Ergebnis:
- Fettiger Ton, der in der Abbildung G (aus dem Deutschen "greesy" - fettig) angegeben ist, reißt praktisch nicht, und wenn das Tourniquet in zwei Hälften gerissen wird, hat die Lücke tropfenförmige Enden.
- Ton mit normalem Fettgehalt (mit N gekennzeichnet) weist eine rissige obere getrocknete Schicht auf, und nach dem Brechen des Tourniquets beträgt seine Dicke am Trennpunkt etwa ein Fünftel des Originals. Dies sind die Proben, die wir auswählen müssen.
- Trockener (magerer) Ton, bezeichnet als L (von deutsch "mager" - mager), wird durch die maximale Anzahl tiefer Risse gekennzeichnet und hat, wenn er gebrochen ist, die größte Fläche an der Stelle, an der die Stücke des Wergs getrennt werden .
In der Regel bleiben nach der Auswahl mehrere (meist 2 oder 3) scheinbar passende Muster übrig.
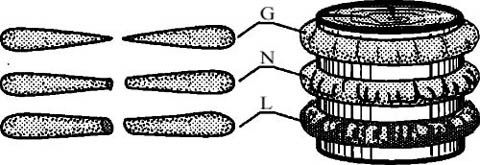
Bestimmung des Fettgehaltes von Ton
Getrocknete Kugeln und Kuchen helfen uns beim abschließenden „Tonguss“. Wir lassen Proben aus einer Höhe von einem Meter über dem nackten Boden fallen. Die haltbarsten von ihnen zeigen die erforderliche Konsistenz von Sand und Ton an. Wenn nach einem Sturz aus einem Meter alle Proben intakt geblieben sind, beginnen wir, die Höhe allmählich zu erhöhen, bis wir die haltbarste von ihnen bestimmen können.
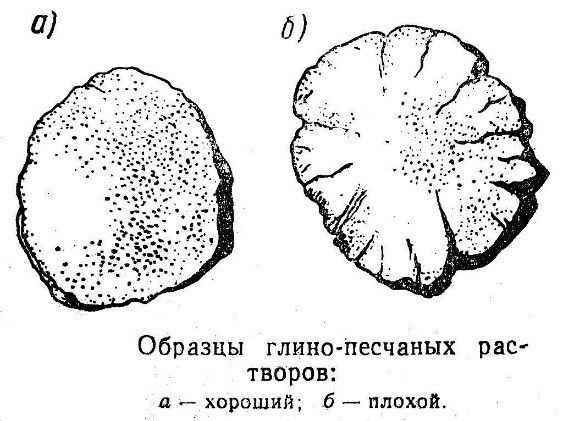
Überprüfung des Lehm-Sand-Mörtels am Beispiel einer Torte
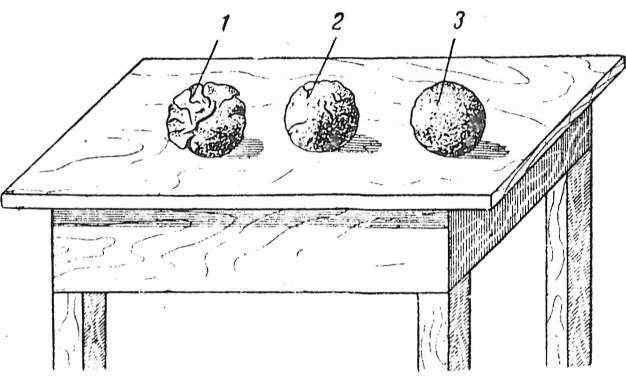
Überprüfung der Qualität eines Ton-Sand-Mörtels am Beispiel einer Kugel
Der nächste Schritt bei der Vorbereitung des Mörtels zum Verlegen des Ofens ist die Berechnung des erforderlichen Verhältnisses von Wasser zum Sandanteil in der Mischung. Die physikalischen Grenzen, innerhalb derer die Tonmischung einen normalen Fettgehalt haben wird, sind ziemlich weit. Da wir den Ofen für uns selbst bauen, besteht unsere Hauptaufgabe darin, die Konstruktion so stark wie möglich zu machen, mit hervorragenden Indikatoren für die Gasdichtigkeit des Materials der Verbindungsnähte.
Zunächst sieben wir den Ton, der bei der Probenahme zurückbleibt. Wir drücken den Ton durch ein Sieb mit kleinen Zellen, damit er sich gleichmäßig mit dem Sand vermischt. Fügen Sie die erforderliche Menge an vorbereitetem gewaschenem Sand hinzu. Wir haben die Anteile von Sand und Ton früher durch die Experimente gelernt. Wir fangen an, Wasser hinzuzufügen und die Lösung allmählich zu kneten. Denken Sie daran, dass Wasser die Härteparameter erfüllen muss, über die wir zuvor gesprochen haben.
Als nächstes nehmen wir eine Kelle in die Hand und machen eine Mulde auf der Oberfläche der gemischten Lösung.
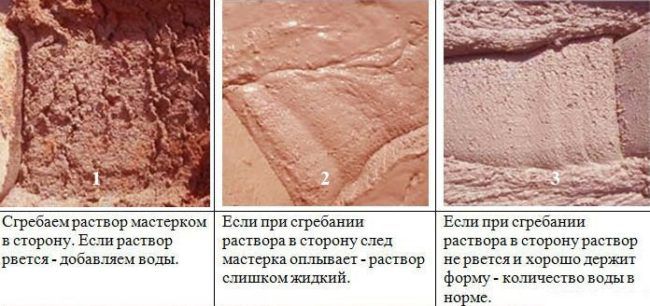
Die Spur von der Kelle (Kelle) hilft dabei, die Bereitschaft der Lösung zu bestimmen
- Eine aufgerissene Mulde zeigt an, dass nicht genügend Wasser vorhanden ist (Abb. 1)
- Wenn die Mulde unmittelbar hinter der Kelle zu schwimmen beginnt, haben sie sie mit Wasser übergossen (Abb. 2). Wir verteidigen die Lösung, entfernen den Schlamm in einer separaten Schüssel. Der Volumenunterschied zwischen dem eingefüllten Wasser und dem ausgepressten Schlamm zeigt uns das erforderliche optimale Verhältnis.
- Wenn Sie sofort mit der erforderlichen Wassermenge raten, hinterlässt die Kelle eine klare, gut unterscheidbare, gleichmäßige Markierung mit hervorgehobenen Kanten auf der Oberfläche der gemischten Lösung (Abb. 3).
Proportionen und richtige Zubereitung von Lehmmörtel, Festigkeitsprüfung
Um herauszufinden, ob unser Lehmmörtel ausreichend stark ist und die erforderliche Haftung hat, ermöglicht der sogenannte Kreuztest. Diese letzte Erfahrung wird zeigen, wie korrekt die Ergebnisse aller unserer vorbereitenden Materialprüfungen waren und wie gut wir die Bestandteile der Ofenmischung gereinigt haben.
Zur Kontrolle brauchen wir ein paar Ziegel, von denen wir einen flach auf den Boden legen und seine größte Fläche (das sogenannte „Bett“) mit einer dünnen Schicht des vorbereiteten Test-Lehmmörtels bedecken. Wir legen einen zweiten Ziegel darauf und lassen die Mischung, nachdem wir sie mit einer Kelle angeklopft haben, etwa trocknen zehn Minuten. Danach greifen wir mit den Fingern nach dem Stein, der sich oben befindet, und ziehen ihn hoch. Nachdem wir es auf eine bestimmte Höhe angehoben haben, schütteln wir die Struktur mit Gewicht: Wenn sich der untere Ziegel nicht gleichzeitig löste, bedeutet dies, dass alle Vorbereitungsarbeiten sorgfältig durchgeführt wurden und wir alle Anteile des Lehmmörtels richtig berechnet haben .
Wenn Sie die einzelnen Details zur Vorbereitung des Mörtels für die Verlegung des Ofens immer noch nicht verstehen, empfehlen wir Ihnen, sich dieses Video anzusehen:
Richtige Vorbereitung des Mörtels zum Verlegen des Ofens: Videolektion
Video: So bereiten Sie eine Tonzusammensetzung zum Verlegen eines Ofens vor